As a critical element of Supply Chain management, safety stock is necessary to ensure smooth operations in many companies. Its role is to mitigate all risks of inventory management disruption: demand behavior, shortages, production delays, supply delays, etc. While having a buffer is important to be able to respond effectively to the variability of demand, it is important to avoid overstocking. For safety stock to be an asset rather than a liability for a company, it is essential to define its ideal level. Lucas Gaurichon, Supply Chain Manager at IZIPIZI, shares his experience on this topic.
Balancing service level and tied-up cash: a strategic trade-off
In case of stockout, the service level declines because the customers must, at best, wait for the product to be available again, or, at worst, make their purchase from a competitor. The service level is therefore naturally linked to the company’s inventory management. To achieve an outstanding service level, a brand must be able to compensate for any stockout in the shortest possible time. It is therefore necessary to set up a safety stock from which to draw to manage the contingencies of demand and sourcing. However, if a high level of safety stock also means a high level of tied-up cash.
This implies that reaching a certain level of service is done at the expense of your cash ratio because a high level of cash is tied up in large safety stocks. Unfortunately, this complex equation has the particularity of being exponential. Indeed, improving the service level by only a few percent, heavily impacts the inventory level and the financial balance. The balance between service level and tied up cash is a strategic trade-off because it involves financial and customer satisfaction issues. Therefore, defining a safety stock strategy must be a collaborative effort between Supply Chain, Finance and Sales departments with the arbitration of the executive management.
The importance of differentiating your safety stocks by product category
Depending on how often products are sold and used, and how important they are to your business, not all of them will require the same inventory coverage strategy. Whether it is from the perspective of a simple ABC class (volume or sales), or from the perspective of erraticity (often referred to as XYZ), or by taking a more complex approach by mixing the two, the categorization of products according to their sales behavior is strategic in many ways.
Primarily, because the human brain cannot manage such a large amount of information (thousands of items, hundreds of thousands of sales, …), classification makes it possible to organize this mass of information on a single level and thus organize products in “boxes”. Secondarily, from a Supply Chain perspective, not every product category will require the same inventory strategy or attention. Obviously, non-strategic items that sell very little will not have the same management rules as those that are key to your business and more importantly, they will not require the same attention from the planner!
Thus, the so-called “strategic” products will potentially have a proportionally “boosted” safety stock calculated to minimize stockouts as much as possible. Conversely, “non-strategic” products, which represent a lesser stake (a stockout being less damaging to sales and brand image), will have a proportionally lower safety stock calculated to minimize or avoid costly overstocking and tied-up cash.
In addition to categorization by sales, it is necessary to differentiate products by their stage in the life cycle. Regardless of their importance in your product portfolio, a product at the end of its life cycle will follow a destocking strategy, so the safety stock will be reduced to a minimum.
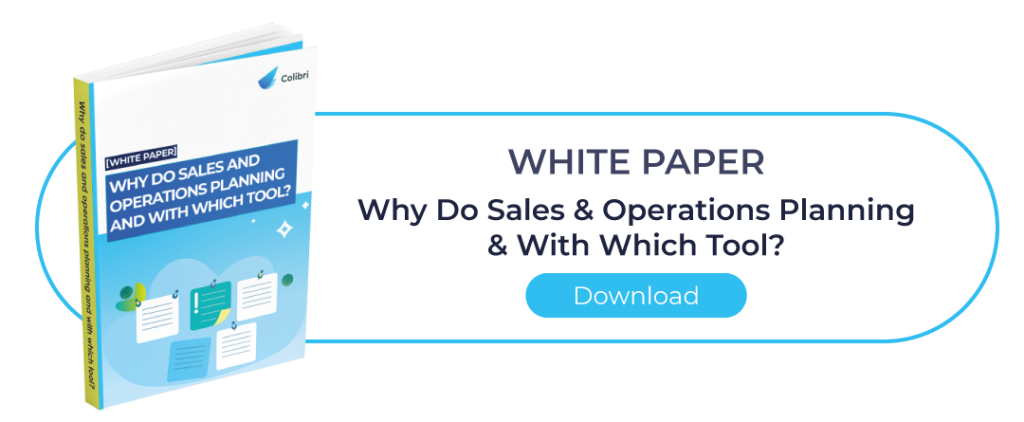
Implementing dynamic safety stocks: an adaptive safety stock management to adjust to variability
“The current complexity of safety stock management is due to the fact that product lines are getting wider and product life cycles are getting shorter. We have to deal with a lot of variability.” says Lucas Gaurichon. To deal with this situation effectively, it is very important to adopt a dynamic approach, which makes it possible to adapt to variability and therefore to modify the level of safety stocks.
The dynamic approach is achieved by specifically analyzing four sources of variability:
– Seasonality: are the products subject to strong seasonality?
– Supplier lead times: what are supplier lead times and potential delays?
– Forecast accuracy: Do we have a contingency plan in case of forecast inaccuracy or activity evolution?
– Variability: is the forecast similar from one month to the next?
Setting up dynamic safety stocks allows your organization to adapt to variability by reviewing stocks according to the contingencies of the process. The more a reference is subject to variations, the higher the safety stock must be to anticipate these variations. By calculating the variability of your products, you can control your safety stock levels. Be careful, however, depending on the market in which you operate, it may be important not to give the same weight to sales data that is too old.
It is not a magic recipe, but rather a pragmatic approach that you need to apply. It all starts with a relevant segmentation of your products according to the criteria that are important for your business (classification A, B, C or X, Y, Z). It is also important to identify the factors that strongly influence your ability to meet demand: product variability, supplier reliability, etc. It is also important to use the appropriate tools to be able to calculate these safety stocks frequently and en masse.
Choosing Colibri to evaluate the ideal inventory level
Colibri is a new generation Demand and Supply Planning solution that helps you find the ideal inventory level for each product reference. With the tool’s FLOW module you can isolate items and groups of items according to their sales behavior and apply specific safety stock strategies. If the tool offers an A, B and C categorization, it achieves a greater degree of precision by setting degressive ratios on all references. The ratios are applied linearly, so as to adapt to the specificities of each product. Colibri can also help you set up dynamic safety stocks by analyzing the life cycles of your products and their variability.
In order to find its ideal inventory level – among other things – IZIPIZI chose Colibri’s VISION and FLOW modules. The VISION module is a collaborative and flexible Demand Planning solution, while the FLOW module is a Supply Chain Planning platform, providing a global vision of the inventory forecasts, with inputs and outputs.
Lucas Gaurichon, Supply Chain Manager at IZIPIZI, is delighted with this collaboration: “Thanks to COLIBRI, we have a better control of our stocks and orders. With this tool, we can forecast both, allowing Finance the necessary vision for a better management of the company. We are very satisfied with the work done with Colibri, it is an agile solution, adapted to growing SMEs, which perfectly meets our Supply Chain challenges.”
Want to know more about how Colibri can help you reach your ideal inventory level? Contact us for more information!